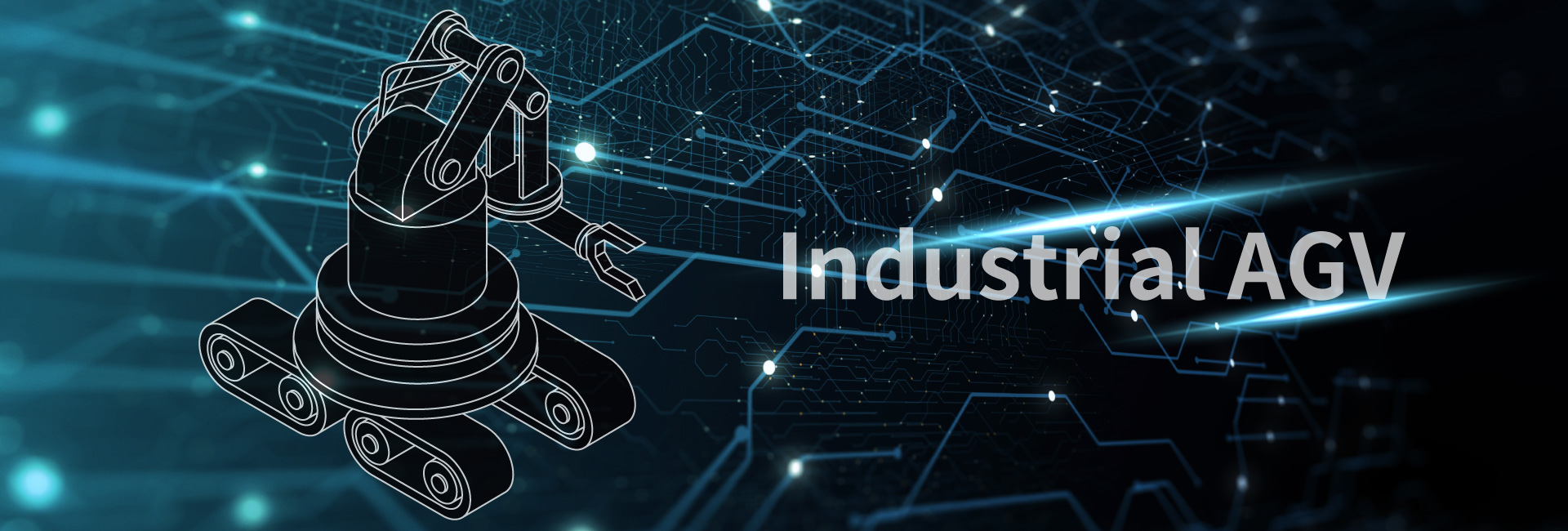
Industrial AGV
AGV, short of Automated Guided Vehicle, also known as unmanned vehicle, is currently an important aspect of industrial automation and is widely utilized in factories and warehouses to fulfill material upload, offload, removal, storage, and transportation. In the wake of Industry 4.0, the emergence of smart factories, and the propagation of smart manufacturing, industrial AGVs have come under more spotlight. According to research, only 5% of the product manufacturing process is dedicated to manufacturing, as the remaining 95% are spent on storage, loading, standby for processing and delivery. Therefore, the introduction of AGV can help cut down on wasted time and raise the overall productivity while dramatically reducing labor cost, making manufacturing layout more efficient, and ultimately lowering operational cost.
The most commonly seen types of AGVs in automated factories include Shelf-Draft, Fork-Lift, Lift-Up, Conveyor, Delivery, and so forth. Some AGVs may be equipped with Cobot (Collaborative Robot) to integrate with the human workforce.
Industrial AGVs are autonomously piloted while towing freight to reach the designated locations through pre-set routes before managing the (un-)loading operations. AGVs are utilized to execute the aforementioned simple repetitive tasks without any requirement for decision making, which means minimum human interventions. For working environments related to warehousing and logistics, or the transportation of corrosive, hazardous, and large-size objects and materials, AGVs can be utilized to optimize working efficiency while minimizing vocational hazards for the working personnel.
As AGVs are configured with designated routes, they need to be re-configured should the paths need to be modified. Although AGVs can detect obstacles, they are unable to take detours around the obstacles, hence they are limited in deployment flexibility. As a result, the application of AGVs in factories is limited to mega-factories with large yield volume with stable production line arrangements such as semiconductor and display-panel plants, instead of smaller factories that require flexibility in production line arrangement and of the commercial applications with irregular routing.
In order to not be limited by the fixed routing of AGVs, many major manufacturers have entered into the development of AMR (Autonomous Mobile Robot), the laser-guided transporter featuring autonomous positioning and automatic navigation. Through its sensors, AMR detects the surrounding working environment and autonomously plans the best routes around obstacles with less limitation to its operating domains. AMR is superior to AGV in its capability to fulfill more complex and cumbersome commands; hence, it can meet the demands of broader application scope and industries. Furthermore, if complemented with real-time edge-computing communication technology such as DDS (Data Distribution Service), it enables AMRs to communicate with one another for collaborative operation for better mobility and higher productivity. It is conceivable that given the advancement in sensor technology, AMRs that can shuttle amongst multiple work-stations would surely be the developmental benchmark for future smart automated manufacturing with customized low-volume and diverse variant production modes.
Industrial AGV Working Flow Chart
Industrial AGVs and AMRs place a high premium on ride stability and working efficiency, with basic features such as anti-collision recognition for personnel and objects, positioning and navigation, freight transportation and identification, and so forth. Moreover, as an integral part of the production line operation, AGVs and AMRs sometimes need to coordinate their operation with other automation equipment, and given the rapid development in IoT, they will be integrated with production equipment of different functions, in sync with diverse production procedures; hence, the requirements for system dispatching, system stability, and positioning precision are high. For AGVs and AMRs featuring SSDs, they can deliver an increase in system stability as SSDs operate without the concerns for collision and shock unlike the conventional HDD hard-disks. The industrial-grade SSDs produced by Solid State Storage Technology Corporation comply with the Anti-Vibration standard of the US military standard, MIL-STD-810G, and Anti-Shock standard of the US military standard, MIL-STD-202G and MIL-STD-883, making them an ideal storage solution for industrial AGVs and AMRs.
SATA SSD
40GB / 80GB / 160GB / 256GB / 320GB / 640GB
NAND Flash: 3D pSLC(TLC)
Interface: SATA 3 (6Gb/s)
Sequential Read: UP to 550 MB/s
Sequential Write: UP to 510 MB/s
SATA SSD
120GB / 128GB / 256GB / 480GB / 512GB / 960GB / 1024GB / 2048GB
NAND Flash: 3D TLC NAND Flash
Interface: SATA 3 (6Gb/s)
Sequential Read: UP to 550 MB/s
Sequential Write: UP to 510 MB/s
NVMe™ SSD
80GB / 160GB / 320GB
NAND Flash: 3D pSLC(TLC)
Interface: PCIe® Gen4 x4
Sequential Read: UP to 3700 MB/s
Sequential Write: UP to 2600 MB/s
NVMe™ SSD
40GB / 80GB / 160GB / 320GB / 640GB /1280GB
NAND Flash: 3D TLC NAND Flash
Interface: PCIe® Gen3 x4
Sequential Read: 3,100 MB/s
Sequential Write: 1,500 MB/s
NVMe™ SSD
40GB / 80GB / 160GB / 320GB / 640GB /1280GB
NAND Flash: 3D TLC NAND Flash
Interface: PCIe® Gen3 x4
Sequential Read: 3,100 MB/s
Sequential Write: 1,500 MB/s
NVMe™ SSD
80GB / 160GB / 320GB
NAND Flash: 3D TLC NAND Flash
Interface: PCIe® Gen4 x4
Sequential Read: UP to 3,500 MB/s
Sequential Write: UP to 2,100 MB/s
NVMe™ SSD
128GB / 256GB / 512GB / 1024GB / 2048GB /4096GB
NAND Flash: 3D TLC NAND Flash
Interface: PCIe® Gen3 x4
Sequential Read: 3,100 MB/s
Sequential Write: 1,500 MB/s
NVMe™ SSD
128GB / 256GB / 512GB / 1024GB / 2048GB /4096GB
NAND Flash: 3D TLC NAND Flash
Interface: PCIe® Gen3 x4
Sequential Read: 3,100 MB/s
Sequential Write: 1,500 MB/s
NVMe™ SSD
256GB / 512GB / 1024GB / 2048GB
NAND Flash: 3D TLC NAND Flash
Interface: PCIe® Gen4 x4
Sequential Read: UP to 6,800 MB/s
Sequential Write: UP to 4,800 MB/s
NVMe™ SSD
240GB / 256GB /480GB/ 512GB / 960GB/ 1024GB
NAND Flash: 3D TLC NAND Flash
Interface: PCIe® Gen4 x4
Sequential Read: UP to 3,700 MB/s
Sequential Write: UP to 2,600 MB/s
NVMe™ SSD
256GB / 512GB / 1024GB
NAND Flash: 3D TLC NAND Flash
Interface: PCIe® Gen4 x4
Sequential Read: UP to 3,700 MB/s
Sequential Write: UP to 2,600 MB/s
NVMe™ SSD
128GB / 256GB / 512GB
NAND Flash: 3D TLC NAND Flash
Interface: PCIe® Gen3 x4
Sequential Read: UP to 2,000 MB/s
Sequential Write: UP to 1,100 MB/s
NVMe™ SSD
128GB / 256GB / 512GB/ 1024GB
NAND Flash: 3D TLC NAND Flash
Interface: PCIe® Gen3 x4
Sequential Read: UP to 2,000 MB/s
Sequential Write: UP to 1,100 MB/s
NVMe™ SSD
128GB / 256GB / 512GB
NAND Flash: 3D TLC NAND Flash
Interface: PCIe® Gen3 x4
Sequential Read: UP to 3,700 MB/s
Sequential Write: UP to 2,600 MB/s
SATA SSD
128GB / 256GB / 512GB / 1024GB
NAND Flash: 3D TLC NAND Flash
Interface: SATA 3 (6Gb/s)
Sequential Read: UP to 550 MB/s
Sequential Write: UP to 510 MB/s
SATA SSD
128GB / 256GB / 512GB
NAND Flash: 3D TLC NAND flash
Interface: SATA 3 (6Gb/s)
Sequential Read: UP to 550 MB/s
Sequential Write: UP to 450 MB/s
SATA SSD
128GB / 256GB / 512GB
NAND Flash: 3D TLC NAND Flash
Interface: SATA 3 (6Gb/s)
Sequential Read: UP to 550 MB/s
Sequential Write: UP to 450 MB/s
NVMe™ SSD
128GB / 256GB / 512GB
NAND Flash: 3D TLC NAND Flash
Interface: PCIe® Gen3 x4
Sequential Read: UP to 2,000 MB/s
Sequential Write: UP to 1,100 MB/s
SATA
128GB / 256GB / 512GB / 1024GB
NAND Flash: 3D TLC NAND Flash
Interface: SATA 3 (6Gb/s)
Sequential Read: UP to 550 MB/s
Sequential Write: UP to 510 MB/s
SATA SSD
128GB / 256GB / 512GB / 1024GB / 2048GB
NAND Flash: 3D TLC NAND Flash
Interface: SATA 3 (6Gb/s)
Sequential Read: UP to 550 MB/s
Sequential Write: UP to 510 MB/s
SATA SSD
128G / 256GB / 512GB / 1024GB / 2048GB
NAND Flash: 3D TLC NAND Flash
Interface: SATA 3 (6Gb/s)
Sequential Read: UP to 550 MB/s
Sequential Write: UP to 510 MB/s